Boston Children’s Simulator Program steps up during COVID-19
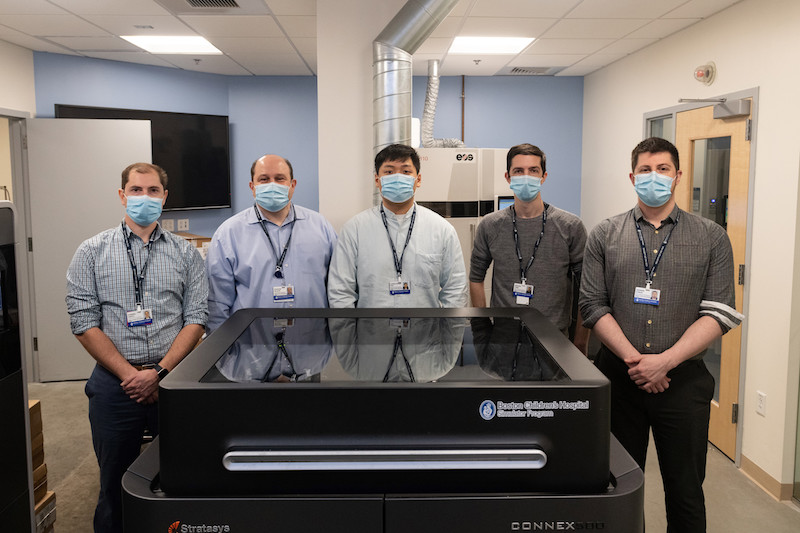
In the early days of the COVID-19 pandemic, hospitals scrambled to adapt and prepare. Amid the chaos, the Boston Children’s Hospital Simulator Program, SIMPeds, sprang into action.
SIMPeds is a world leader in running live simulations of care scenarios, allowing health care providers to rehearse tough or unanticipated situations in advance. Its SIMEngineering division is a leader in the rapid prototyping of medical devices, anatomic models to train clinicians on rarely-used procedures, and models that replicate an individual patient’s anatomy to help surgeons plan difficult operations.
When COVID-19 hit, SIMEngineering quickly began producing personal protective equipment (PPE) and other helpful items on its 3D printers — everything from custom shields to nasal swabs and ear protectors for N-95 mask wearers.
“Over 14 weeks, the team completed 36 requests for device solutions,” says Stephen Wilson, SIMPeds director of development engineering. “We were inspired by the people and teams looking to collaborate and problem-solve.”
Thanks to the hospital’s supply chain management group, Environmental Health & Safety, and others, Boston Children’s was able to get enough PPE through official sources and careful reuse. But SIMEngineering’s efforts weren’t for naught.
“A safety net of workable solutions was put in place, but thankfully we never had to use it,” says Wilson.
PPE for clinical simulations and more
While not needed for patient care, the PPE solutions have been put to good use in staff training around COVID-19 care. SIMPeds has staged a series of simulations to help clinicians practice donning and doffing PPE and adapt to new COVID-19 protocols and reconfigured work spaces.
“We unearthed all the things that needed to change, and built a variety of process scenarios around the COVID response,” says Gabe Arato, SIMPeds program manager for strategy and business development. “We implemented these clinically at Boston Children’s and shared them with partner institutions.”
Here’s a sampling of what SIMEngineering created:
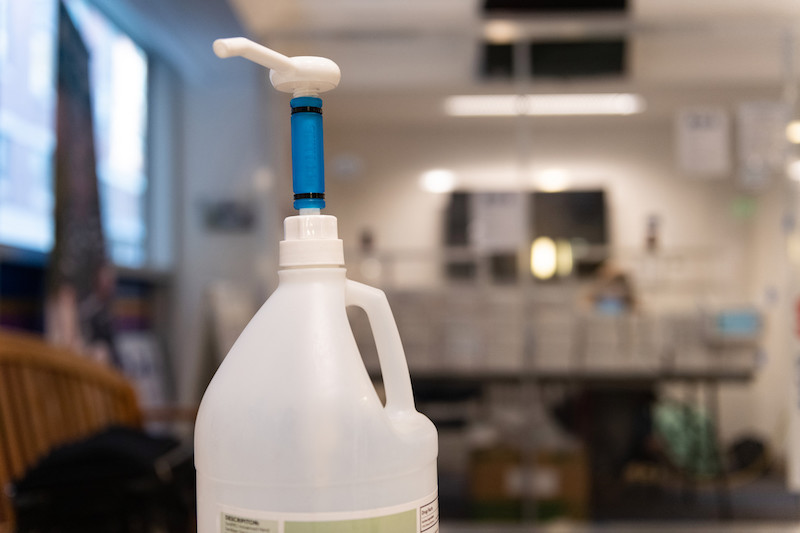
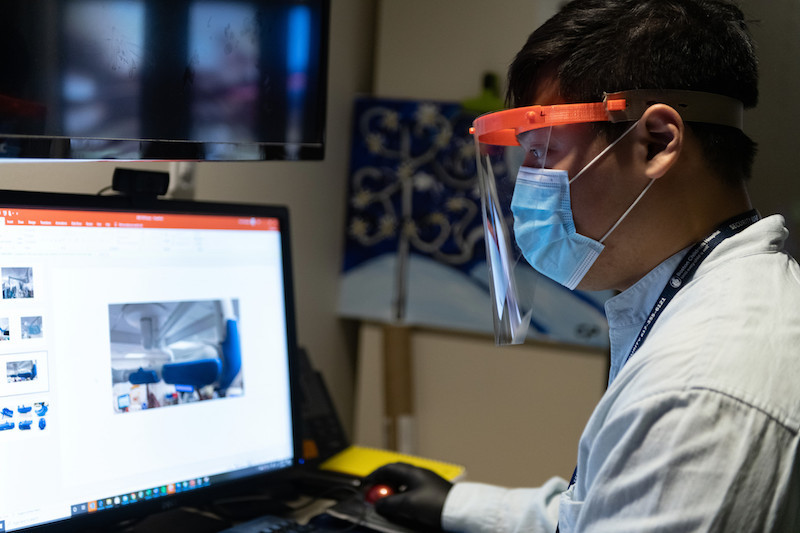
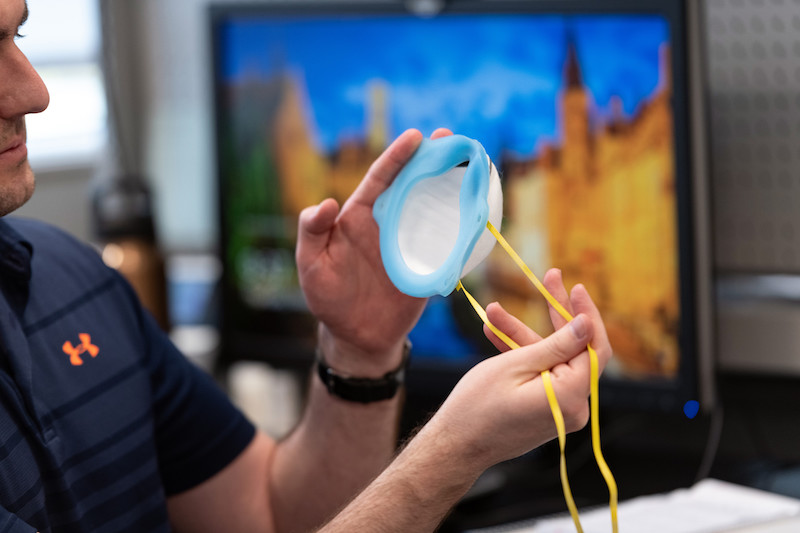
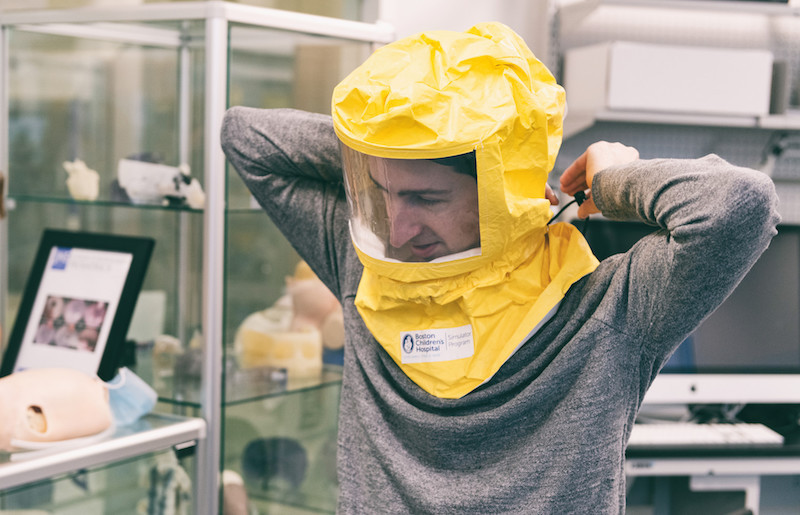
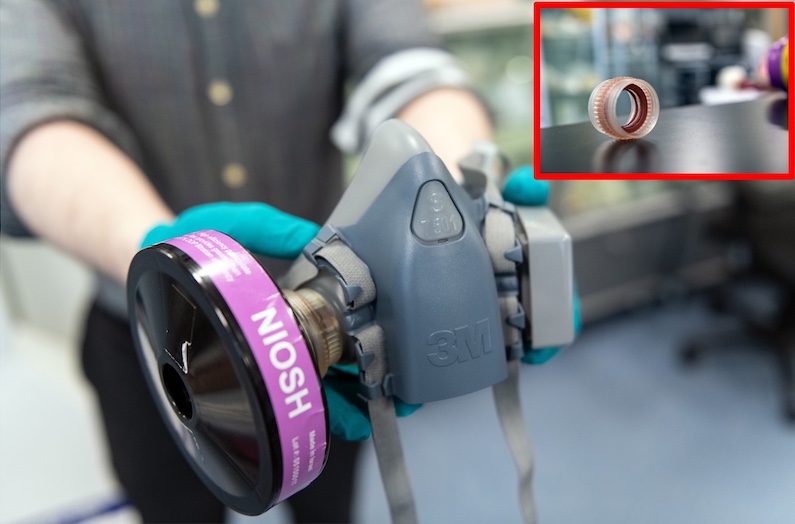
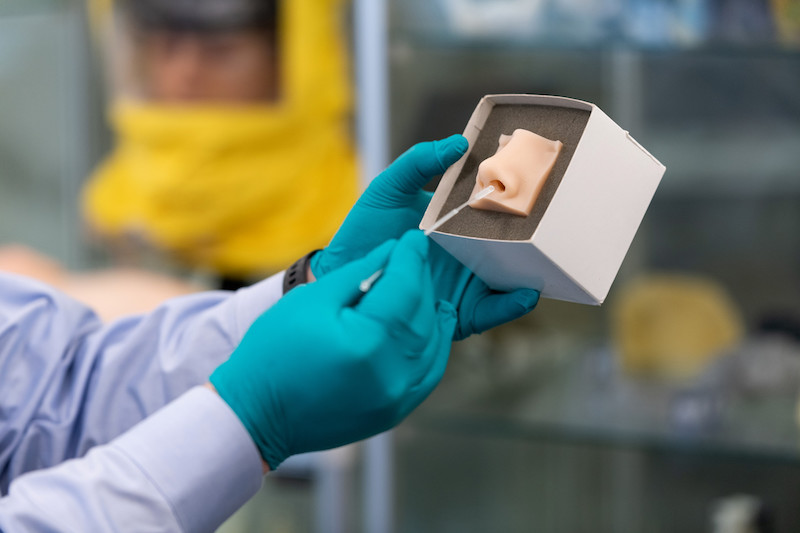
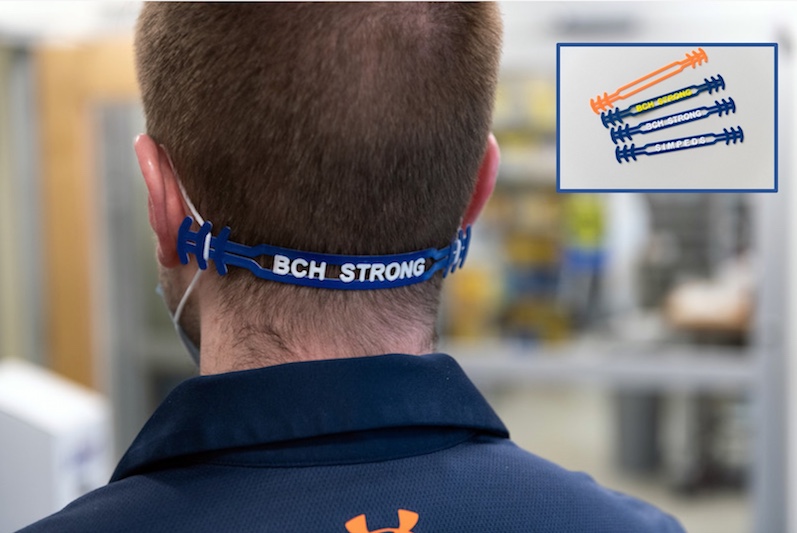
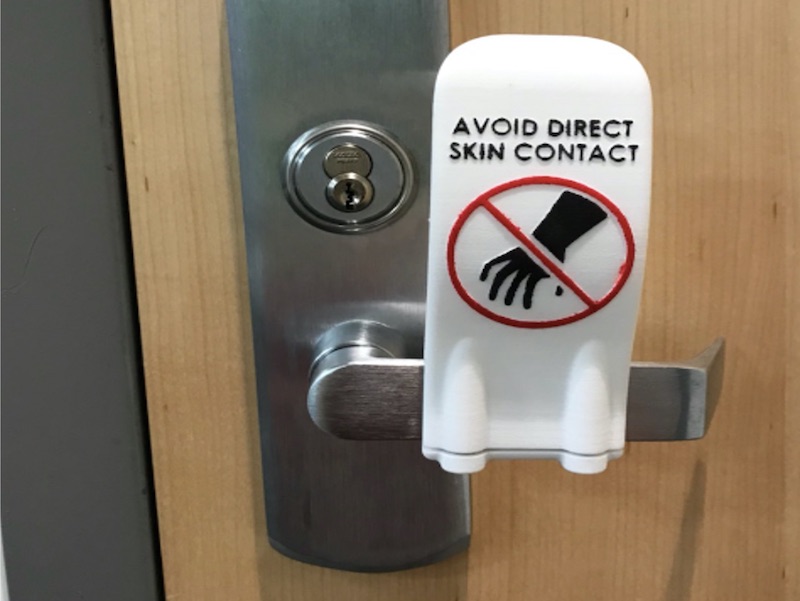
A COVID-19 safety net
While not all items made the cut or were ultimately needed, SIMPeds and SIMEngineering helped Boston Children’s be prepared during a frightening time.
“By collaborating closely with Supply Chain Management and Environmental Health & Safety, we were able to direct our efforts to the areas of greatest risk,” says Wilson. “Creating actionable contingency plans conveyed a sense of control.”
“Without the ability to use this equipment for simulations, the learning curve would have been much steeper,” adds Arato. “We couldn’t have been so nimble; we couldn’t have scaled up clinical operations so rapidly.”
Learn more about SIMPeds and SIMEngineering.
Related Posts :
-
Which pain medication is right for your child? What a pediatrician wants parents to know
There’s no shortage of safe and effective pain medications for children. Acetaminophen (commonly known as Tylenol), ibuprofen (Motrin, Advil), ...
-
AI-enabled medical devices are burgeoning, but many haven’t been tested in children
Medical devices that incorporate artificial intelligence and machine learning are proliferating. In 2013, the FDA approved fewer than 10 such devices; by 2023, ...
-
Model enables study of age-specific responses to COVID mRNA vaccines in a dish
mRNA vaccines clearly saved lives during the COVID-19 pandemic, but several studies suggest that older people had a somewhat reduced ...
-
New insight into the effects of PPIs in children
Proton-pump inhibitors (PPIs) are frequently prescribed to suppress stomach acid in patients with gastroesophageal reflux disease (GERD). Prescribing rates of ...